Bon j’ai décider de commencer l’article avant que toutes les façades ne soient terminées parce que sinon, vous n’êtes pas près de lire l’article !
J’ai donc été chercher une bille de chêne de 21mm d’épaisseur…
pour faire des façades de ce style :
C’est à dire les petites hauteurs d’un seul tenant, et les grandes d’une façon plus classique avec un assemblage profil / contre profil ou tout au moins tenon / mortaise.
J’ai commencé par les 4 petites, voici le résultat :
Pour la finition j’ai choisi de l’huile pour essayer de garder un contact avec la matière. Le résultat est plus foncé que je pensais, mais ça me plait.
Pour la tranche, j’ai choisi de faire un chanfrein de 2mm sur les 4 cotés des façades.
Moi aussi je vais bientôt proposer un tag fond d’écran ! 😉
Vous aurez donc le droit à la suite des façades dans ce même article…
MAJ 18 septembre 2009 : la suite !
j’ai acheté une machine à bois pour cette étape : la réalisation des facades de la cuisine. J’ai fait le choix de prendre mon temps pour ne pas me blesser mais surtout pour apprécier ces moments où l’on est seul avec la matière (!).
Dernièrement, je suis tombé sur un article de l’atelier bois (n°144 page 55-59) décrivant la conception d’une cuisine dans un espace comportant des contraintes, j’avais l’impression que l’on parlait de ma cuisine, « un coté à 40cm, un autre à 60cm à cause du manque de place », « des facades sur mesure pour des placards sur mesure »… Le dessin des facades est aussi très proche, tenons-mortaises, rainures, contre plaqué, chanfreins.
Les étapes de la réalisation des facades sont les suivantes :
– tracages
– sciage
– dégauchissage
– rabotage
– tenons
– mortaises
– rainures
– chanfreins
– ponçage
– découpage des fonds
– assemblage collage
– vernis
– pose
– montage des poignées
En chiffre, c’est
- 25 façades
- 101 montants
- 3m² de contreplaqué chène
- 102 mortaises, 102 tenons
- 1200 chanfreins
- quelques dizaines d’heures de boulot !
Une fois dégauchis et rabotés, j’ai toute de suite coupé les éléments à la bonne longueur à la scie circulaire sur table avec une lame carbure 48 dents : résultat impeccable !
Ensuite place aux mortaises : j’ai utilisé la mortaiseuse à Bedane Fox Delta, en gros, c’est une perceuse à colonne qui fait des trous carrés !
En vidéo
Une fois les reglages faits, ça va relativement vite ! Voilà le résultat sur une planche test : c’est net, précis. Rien à voir avec les mortaiseuses de bout d’arbre, en plus il faut arrondir les tenons !
Maintenant que les trous sont faits, passons aux bosses : les tenons
Je les ai fait à la toupie :
Une partie du résultat :
Il a fallu passer 3 fois par tenon : une fois pour le dessus et de dessous puis une fois pour chaque coté.
Pour les rainures, j’ai utilisé deux systèmes : la toupie sur table et la défonceuse.
La toupie pour les éléments débouchants, la défonceuse pour les autres (sinon, pas de presseur sur la toupie)
De même pour les chanfreins, j’ai utilisé les deux procédés, la toupie pour les éléments en longueur et la defonceuse pour les autres, trop dangereux à mes yeux à faire à la toupie.
Ensuite vient le découpage des éléments en contre plaqué chêne
Pour optimiser ce découpage, j’ai utilisé un logiciel en version démo : opticoupe
Il permet, une fois ses surfaces renseignées, d’optimiser le tracé.
Le tracé comprennant l’epaisseur de la lame de scie.
Passons à l’assemblage après un ponçage manuel minucieux (180, 220, 320, 600)
Pression pendant le collage, mais les tenons / mortaises sont tellement ajustés que de toute façon, ça ne bougeait plus une fois serrés.
Je n’avais pas de serre joint assez grand pour récuperer le petit défaut d’equerrage, j’ai donc procédé à un serrage original pour cette façade…
J’aime beaucoup l’effet du chanfrein qui renforce l’idée de l’assemblage et qui masque leur imprecision.
Ensuite, finition : vernis
Puis montage.
Pour les poignées de porte, j’ai fait un gabarit, histoire de ne pas me louper ! Il permet de percer les deux trous pour les poignée à partir du milieu de la façade.
Et voilà le résultat. Pour le montage des façades de tiroirs, j’ai du regler les tiroirs pour que les façades ne touchent pas aux caissons : ça a été long, mais je ne regrette pas d’avoir passé le temps nécessaire.
Pour les portes, la précision des charnières BLUM permet de faire un travail de qualité.
Je dois encore remplacer la planche mélaminée à coté de lave linge par une façade et aménager les plinthes avec des tiroirs à roulettes.
En ce qui concerne la cuisine elle même, il reste trois chantiers :
- deux trous de plus dans le mur pour le verre et les briques alimentaires
- un meuble dans la niche au dessus du micro-onde avec des vitraux réalisés par mon père et peut être un placard à balais à droite en entrant (dans le futur)
- la derniere couche de peinture (et peut être un mur de couleur) que l’on aurait du faire dès le début !
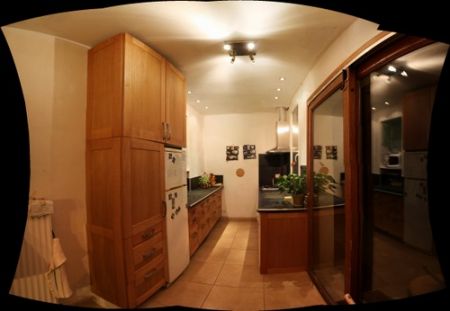
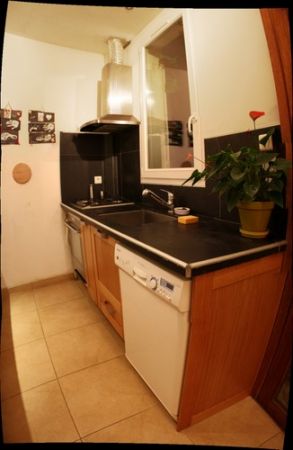
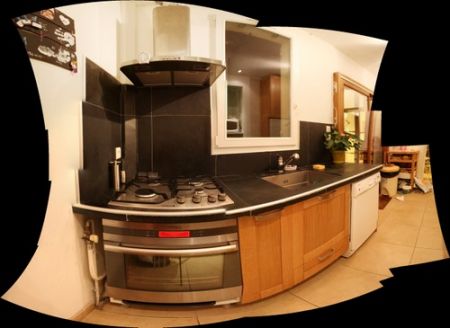
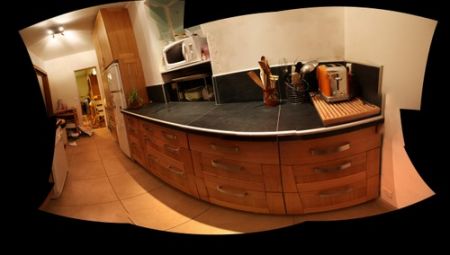